Take heed to this text |

The PPE module examined by gantry robotic will energy the Gateway house station. Supply: Bell-Everman
NASA’s Artemis Program plans to ship people again to the moon to ascertain a lunar floor base and house station. Often known as Gateway, the house station shall be powered by the Energy and Propulsion Ingredient, or PPE, module, which makes use of massive arrays of superior, multi-junction photo voltaic cells to generate 60 kilowatts of energy.
To make sure the PPE’s success, it’s essential to check the photo voltaic arrays with superior simulation that replicates daylight and measures every circuit’s efficiency. Engineered by Angstrom Designs Inc., the photo voltaic simulator heads should be positioned at quite a few factors alongside the size and width of the photo voltaic arrays.
That course of that’s normally achieved utilizing automation frames that encompass linear movement levels. As a result of the PPE’s photo voltaic arrays are so massive, customary frames constructed for standard array sizes couldn’t present the required vertical and horizontal movement.
Bell-Everman designed, engineered and fabricated a customized movement system that allows the Angstrom Designs photo voltaic simulator heads to check the PPE’s photo voltaic panels. And to make sure that the simulator heads are absolutely calibrated, we additionally constructed the I-formation gantry robotic that calibrates and validates the simulator efficiency in opposition to photo voltaic cell requirements.
Right here’s a deep dive into the mechanical challenges of assembly the movement system’s particular necessities.
Bell-Everman finds essentially the most cost-effective design
An early design featured two bending tracks — one on the bottom and the opposite roughly 30 ft. excessive close to the highest of the panels. The tracks would assist the LED photo voltaic simulators — a 3,500-lb. load — permitting them to check one deployed array, then go across the bend and take a look at an array on the opposite aspect of an enormous scaffold construction.
However this answer, which might function like an I-formation gantry, required specialised bearing methods. This elevated design complexity and shortly drove the mission past price range, given the peak and cargo necessities.
As a substitute design, Bell-Everman engineered a movement system that makes use of a cellular base for X and Y motions, and a servo-controlled Z to lift the photo voltaic simulators up a three-story tall vertical tower. This mobile-robot gantry design was essentially the most cost-effective choice and drastically lowered system complexity.
Body, movement system should keep upright
Because of the photo voltaic simulator payload, the whole body of the mobile-robot gantry needed to bear plenty of weight and hold the simulator LED arrays parallel to the photo voltaic array. This required a major quantity of finite component evaluation to make sure the subframe may stand up to the forces of hoisting the load — and survive a seismic occasion with out toppling over.
Additionally, the absolutely constructed movement system is massive and should be capable of make a flip across the finish of a deployment construction in a really tight flooring plan.
Initially constructed to check the PPE’s panels, NASA can proceed to make use of the movement system to check future space-going applied sciences.
Heavy cantilevered lifting handles forces
The 240 photo voltaic simulator heads are nested in a pantographic morphing array in three balanced pivoting segments, which transitions between two preparations: a 2-by-18-ft. grid and a 6-by-6-ft. grid. Because the array actuates, it imparts excessive second forces on the movement system’s body.
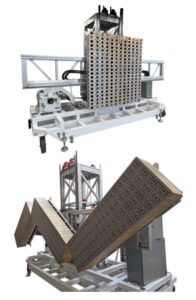
The PPE photo voltaic simulator body’s pantographic morphing array of three balanced pivoting segments homes nested pLEDss heads within the open slots. Supply: Bell-Everman
To accommodate these forces, we used heavier-than-usual linear bearing rails and crossed curler bearings with an 8-in. bore to cross Ethernet communication and 40 kW {of electrical} energy per phase.
The array and morphing construction symbolize a 3,500-lb. cantilevered load on the vertical tower, requiring a counterbalance to each steadiness second hundreds on the tower and supply one thing near impartial buoyancy.
Gross motion of the mixed payload and LED array is supplied by a ten,000-lb. drum hoist. To attain vertical movement, a single ServoBelt Heavy Linear is used with Bosch Rexroth drives and huge redundant cables.
The counterbalance design ensures that the vertical drive solely sees a weight imbalance of fifty to 300 lb. — greater than sufficient respiratory room for the ServoBelt Heavy LoopTrack drive, which might accommodate as much as 600 lb. of linear pressure.
Additionally, because of the counterbalance, any drive failure wouldn’t lead to dropping this precious load. Threading these cables by means of pulley redirects allows the counterweight and payload to be raised collectively to their mid-height from a parked place on the backside.
This fascinating and absolutely redundant cable structure permits full impartial buoyancy all through the vary of the coarse positioning hoist.
Tower constructed piece by piece
The vertical tower supporting the photo voltaic simulator load will attain three tales excessive when absolutely constructed. As a result of it was too tall to suit contained in the constructing the place it was made, the tower was in-built three items.
We made a shorter counterbalance cable set to permit the underside part for use for full useful testing inside the low ceiling of our meeting bay.
Because the elevate travels up the finished vertical tower, any vibrations induced by imperfections the place every part is linked would have an effect on the simulator efficiency and diagnostic high quality. We joined every tower part with a particular multigenerational technique of splicing, just like our long-travel gantry methods. These common splicing joints allow easy vertical movement throughout the splices.
Z-axis automation for getting round
The movement system’s actuation is operated by hand aside from the Z-axis journey, which is absolutely automated. Due to the excessive worth of space-going photo voltaic arrays like this, it is much better to manually transfer axes of movement which have any probability of damaging the array.
An electrical-powered tug pulls the whole system for giant actions, together with when the system is faraway from or put into storage. When the system is introduced close to the PPE photo voltaic array, nice changes are made with lever arms connected to the system’s wheels. When the right place is achieved, screw toes are lowered to the ground.

Totally constructed, the photo voltaic simulator tower reaches three tales. Right here, the pantographic morphing array is present in its six-by-six-foot configuration. Supply: Bell-Everman
Electrical system designed to keep away from flames
As a result of the simulator homes 240 of the 500-watt pLEDss heads, a big problem of this mission was managing over 120 kW of energy.
That includes many breakers and branches, {the electrical} system is designed to stop overheating and fireplace injury ought to shorts happen at any degree.
Calibration system is separate
To make sure that Angstrom Designs’ programmable LED photo voltaic simulators (pLEDss) carry out efficiently, they should be calibrated in opposition to photo voltaic cell requirements referred to as isotypes.
We additionally designed a calibration system for the PPE photo voltaic simulator to check in opposition to, consisting of an I-format gantry that homes the photo voltaic cell isotypes.
Often known as the “Calibot,” this I-frame gantry robotic is able to calibrating the pLEDss heads whereas the system is in both morphing place.
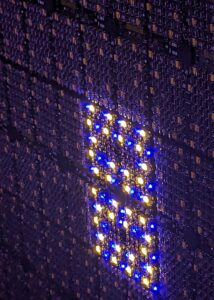
pLEDss heads have full spectral management to present match junctions for cells from single junction as much as six junctions. Supply: Angstrom Designs
When the Calibot is maneuvered to the pLEDss tester, management bins are linked, and docking mechanisms protect the optimum standoff distance throughout calibration. Each the PPE simulator system and the Calibot shall be saved with NASA in the identical facility.
The pantographic morphing array consists of three smaller subarrays that every comprise 80 pLEDss heads. Every subarray has its personal terminal blocks and cables.
Every head’s DC energy provide is delivered 220 VAC to permit the usage of smaller 18-gauge energy wires. Due to the quantity of harnessing, it is very important scale back weight and house for the almost 400 cables working to the breaker bins.
Primarily based on the early I-format gantry design — which wanted to make a U-turn across the assist scaffold holding two photo voltaic arrays, a flooring mounted cable monitor and a information system — the full value for the ability supply alone was estimated to be roughly $200,000.
Due to the mobile-robot gantry design with easy extension cordage, this expense was lowered to $6,000 and solely 150 toes of cable.
All the mission may have been achieved with a big, track-based I-format gantry. However Bell-Everman simplified the design with cellular gantry robots, considerably lowering system complexity and prices.

I-Type linear robots that includes ServoBelt Linear actuators excel at point-to-point movement management. Supply: Bell-Everman